About the introduction of the centrifuge
A brief history In ancient China, people used one end of the rope to tie the clay pot, and the other end of the rope, rotating the pottery jar, and generating the centrifugal force to squeeze out the juice of the berries in the pot, which was an early application of the centrifugal separation principle. Industrial centrifuges were born in Europe. In the middle of the 19th century, there were three-legged centrifuges for textile dehydration and upper-suspension centrifuges for separating crystalline sugar from sugar factories (see Filter Centrifuge). These early Zui centrifuges are batch operated and manually drained. Due to the improvement of the slag discharge mechanism, a continuously operating centrifuge appeared in the 1930s, and the intermittent operation of the centrifuge was also developed due to the realization of automatic control. In 1879, Sweden's CGPde Laval invented a separator that separates butter from milk. Its drum is only a hollow cylinder. Later, the axially stacked conical discs were added to the drum to significantly improve the separation effect and increase the processing capacity. This technological advancement led to the rapid development of the disc separator. The rotation speed of the centrifugal separator gradually develops from low speed to high speed, and the diameter of the drum is also gradually increased, which improves the separation effect and improves the processing capacity.
Classification industrial centrifugal separators are classified into three types according to the structure and separation requirements: filtration centrifuge, sedimentation centrifuge and separator (see table). The separator is only suitable for separating low concentration suspensions and emulsions, including disc separators (see color chart), tube separators and chamber separators.
Principle of Operation The centrifugal separator (Fig. 1) has a cylinder that rotates at a high speed about its own axis, called a drum, which is usually driven by an electric motor. After the suspension (or emulsion) is added to the drum, it is rapidly driven to rotate at the same speed as the drum, and the components are separated under the action of centrifugal force and discharged separately. Generally, the higher the drum speed, the better the separation.
The centrifugal separator has two working principles: centrifugal filtration and centrifugal sedimentation. 1 centrifugal filtration (Fig. 2a): the centrifugal pressure generated by the suspension under the centrifugal force field acts on the filter medium (filter or filter cloth) to make the liquid pass through the filter medium to become the filtrate; and the solid particles are trapped on the surface of the filter medium. The filter residue is formed to achieve liquid-solid separation. The filter drum has a hole in the circumferential wall and is lined with filter media on the inner wall. 2 Centrifugal sedimentation (Fig. 2b): The liquid-solid (or liquid-liquid) separation is achieved by the principle of rapid sedimentation and stratification of the components with different densities (or emulsions) in the centrifugal force field. The circumference of the settling drum has no holes. Figure 3 shows four typical settling drums. After the suspension (or emulsion) is added to the drum, the solid particles (or the denser liquid) settle to the drum wall to form a sediment (or heavy separation liquid). The liquid having a lower density is collected in the direction of the center of the drum, and is discharged to the overflow port to be a separation liquid (or a light separation liquid). The drums in Fig. 3a, c, and d are intermittent slag, suitable for suspension or emulsion separation with smaller particle size and lower concentration of solid particles; the drum of Fig. 3b is continuously slag discharged by spiral, and can be separated A suspension with a higher concentration of solid particles. In a drum having a multi-layered conical disc, the liquid is divided into a plurality of thin layers by the disc, which shortens the distance of sedimentation separation, speeds up separation, and improves separation.
Another type of separator for experimental analysis can perform liquid clarification and solid particle enrichment or liquid-liquid separation with a separation particle size of 0.1 to 0.5 μm. The commonly used test tube separator (Fig. 4) rotates at a speed of 3000 to 20000 rpm. The glass test tube filled with the same amount of liquid is symmetrically inserted into the pocket of the pendulum or angle rotor, and the liquid is settled in the test tube under the action of centrifugal force. . The ultra-high speed analysis separator uses a small diameter sedimentation drum. This type of separator has different structural types for operation under normal pressure, vacuum, and freezing conditions.
Factors Affecting Separation An important measure of the separation performance of a centrifuge is the separation factor Fr. It represents the ratio of the centrifugal force to the gravity of the separated material in the drum. The larger the separation factor, the faster the separation is usually and the better the separation effect. The industrial centrifugal separator has a Fr of 100 to 20,000, the super-speed tubular separator has a Fr of 62,000, and the analytical over-speed separator has a Frzui of up to 610,000. Another factor that determines the processing capacity of the centrifuge is the working area of ​​the drum, which has a large processing capacity.
The filter centrifuge and the sedimentation centrifuge mainly rely on increasing the diameter of the drum to enlarge the working surface on the circumference of the drum; in addition to the circumferential wall of the drum, the separator has additional working surfaces, such as discs and chambers of the disc separator. The inner cylinder of the separator significantly increases the settling face. In addition, the finer the solid particles in the suspension, the more difficult it is to separate, and the fine particles carried away in the filtrate or the separation liquid are increased. In this case, the centrifuge needs to have a higher separation factor to effectively separate. When the viscosity of the liquid in the suspension is large, the separation speed is slowed down. The difference in density between the components of the suspension or emulsion is advantageous for centrifugal sedimentation, while centrifugal filtration of the suspension does not require a density difference between the components.
The choice of centrifuge should be based on the size and concentration of solid particles in the suspension (or emulsion), the difference in density between solids and liquids (or two liquids), the viscosity of the liquid, the characteristics of the filter residue (or sediment), and the separation requirements. A comprehensive analysis was carried out to meet the requirements for the moisture content of the filter residue (sludge) and the clarity of the filtrate (separation liquid), and which type of centrifugal separator was initially selected. Then according to the amount of processing and automation requirements for the operation, determine the type and specifications of the centrifuge, after the actual test by zui. Generally, a filter centrifuge may be used for suspensions containing particles larger than 0.01 mm in size; for fine or compressible deformation of the suspension, a sedimentation centrifuge is preferred; for suspensions, the solid content is low, the particles are minute and the liquid is When the degree of clarity is high, a separator should be used. The filter centrifuge can obtain a drier filter residue and wash the filter residue. Some particles will break when the scraper is used to remove the slag. When a centrifugal separator can not meet several requirements of separation, several centrifugal separators can be used together.
Research and development of centrifugal separator research and development trends are: 1 enhanced separation performance, including increasing the drum speed; adding new driving force in the centrifugal separation process; speeding up the slag speed; increasing the length of the drum to separate the centrifugal sedimentation Prolonged. 2 The development of large-scale centrifugal separators, mainly to increase the diameter of the drum and the use of double-sided drums to improve the processing capacity to reduce the equipment investment, energy consumption and maintenance costs of processing unit volume of materials. 3 Improve the slag discharge mechanism to make the operation continuous. 4 Add dedicated and combined drum centrifuges to meet special and multiple separation requirements. 5 Theoretical research, mainly studies the fluid flow condition and the formation mechanism of filter residue in the drum, and studies the calculation method of small separation degree and processing capacity of Zui. Research on stress distribution and strength calculation of complex shape drums. 6 study the centrifugal separation process Zui Jiahua control technology.
Background music Hoster through wifi, mobile phone APP control, wireless wifi Internet access, support QQ music, cool dog. Can play any music you like without leave your safa, you can control from your mobile app. Wireless video transmission, used in household, office, commercial space, entertainment. Could offer 5 inch screen and 7 inch screen. It is a part of Smart Home system. Make your home comfortable and modern.
Specification
Material: metal edging, capacitive screen
Size: 5.7 inch screen
Communication Frequency: WIFI
Features: Mobile APP control playback, WIFI wireless Internet access, ay music software players, wireless connection LCD TV for video wireless transmission.
Field of Application: homes, offices, commercial space and entertainment.
Can use to home, office, meeting room, any time play music and relax
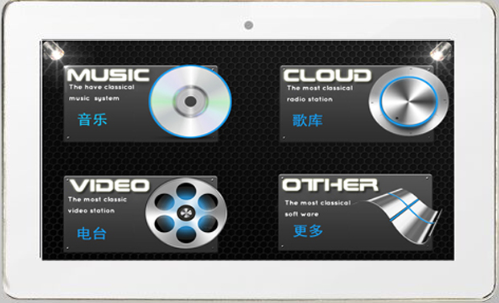
Smart Home Background Music,Smart Home Automation Speaker,Smart Home Automation Background Music Hoster
Shenzhen Zhuohao Intelligent Electronic Development Co., Ltd. , https://www.szactop-smart.com